Our Approach
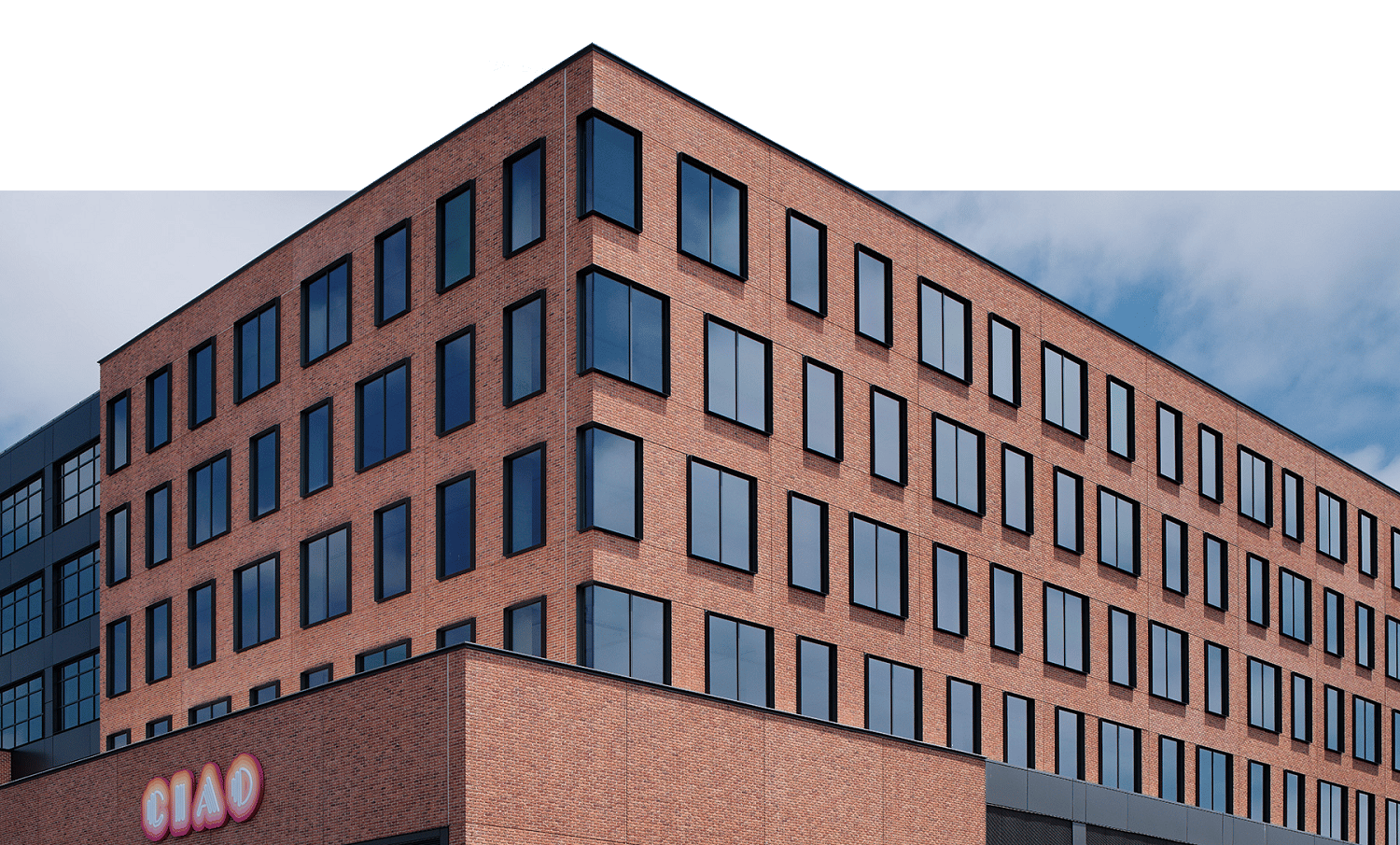
Clark Pacific is the single source of responsibility through collaborative design, advanced manufacturing, and efficient delivery of high-quality and cost-effective prefabricated building systems.
Our offsite manufacturing approach reduces overall project risk through improved cost and schedule certainty as well as greater supply chain controls, without compromising a project’s overall design.
With over five decades of proven experience and industry-leading products, we breathe new life into construction with a smarter, more efficient path from design to project completion.
Leverage Offsite Construction for Better Project Outcomes
Why choose offsite construction? Traditional construction today is risky. Due to labor shortages, material availability, and budget and schedule uncertainty, the risks are high.
Minimize site waste, traffic and provide safer jobsite
Offsite construction improves schedules by 30-50%
Offsite construction provides cost certainty
Manufacturing reduces construction waste and supply chain risks
Take ownership of the asset sooner
Manufacturing delivers quality assurance and control throughout the process
Clark Pacific’s Prefabricated Systems Approach
Leverage Cutting-Edge Technology | Design Through Construction
Our approach to Building Information Modeling (BIM) is personal as a manufacturer. We depend on the latest technology to design for manufacturing (DfMA) and strive for the most efficient design for constructability. Because we are self-performers of work beyond customary build-in-place, our details and constructability feedback are administered with more precision and quality.
Model to Fabrication
Clark Pacific coordinates all the information into models which are leveraged to fully support fabrication, with no intermediate steps in our integrated process.
Below is a brief list of the processes, from model to fabrication, that we leverage:
- Rebar and miscellaneous metal fabrication
- Bill of Materials
Drawings (with no “dress-up” in CAD) - Diagrammatics (Work Instructions)
- 4D site logistics
- Physical site coordination
- Safety information
Let's talk about your next project
Prefabrication is most successful when it is part of the project strategy