PARC
A Turnkey Parking Structure Solution
PARC reduces the complexity of designing and building parking structures and offers owners & developers a more efficient and effective solution. Clark Pacific’s advanced product-based delivery model relies on experienced teams guiding the process from entitlement to hand over.
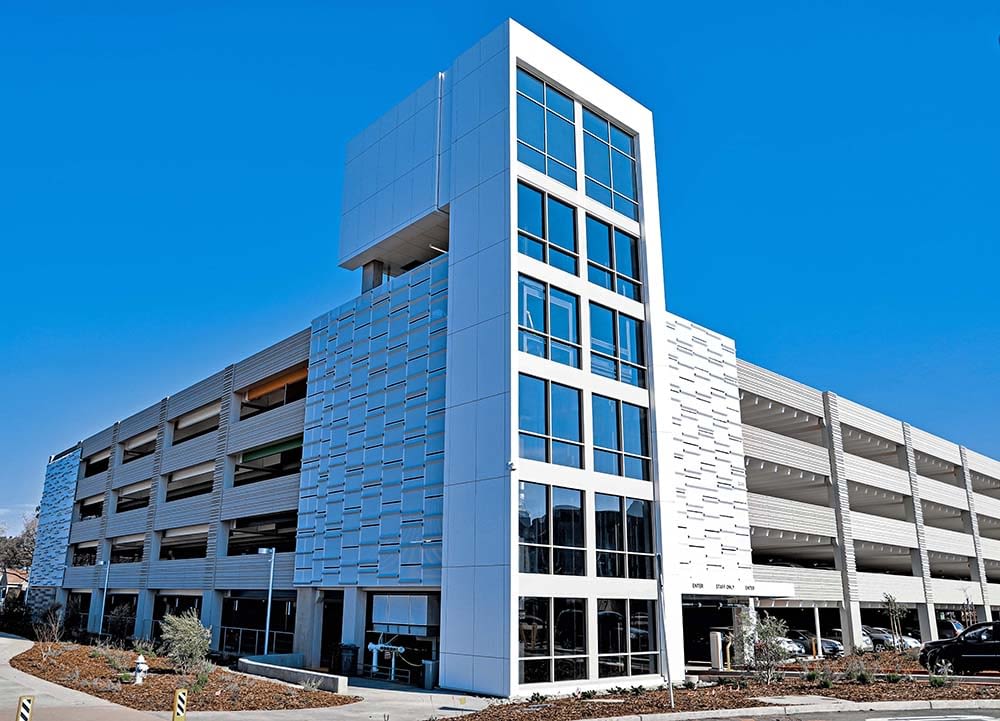
Single source for the entire parking structure
PARC delivers a low-risk, high-quality parking structure with design flexibility at the lowest cost in the shortest amount of time. We make this happen by combining our standardized PARC product with our in-house Design-Build service. Its a winning match – where our clients come out on top!
How does Product-Based Delivery benefit you?
- Complete pre-design based on requirements, standard products & best practices
- Ready to manufacture + build + install
- Easily customized to accommodate unique project-specific requirements
- Smoother path to stakeholder consensus with a single point of contact, entitlements through handover
Benefits of PARC
In house parking consultants and designers
Single warranty for the parking structure
Accelerated schedules: 30%-50% faster than traditional methods
Resilient and adaptable design
Designed for increased safety and better navigation
Utilizes CARBONSHIELD reducing embodied carbon in the structure
CARBONSHIELD™ is a unique and proprietary concrete mix developed by Clark Pacific.
CARBONSHIELD provides the same performance as traditional mixes and is standard in our structural products.
CARBONSHIELD replaces 25% of the portland cement, reducing embodied carbon by up to 20%.
PARC standard scope includes:
- Design-Build services
- All structural framing
- Foundations and retaining walls
- Elevator and stairs
- Fire protection
- Electrical: LED lighting
- Drainage
Prefabrication met all of our prerequisites whereas cast-in-place would have taken longer, cost more, required a greater footprint on site and been very disruptive to Major League Soccer games
Deke Hunter
Hunter Properties